Watch for Common Threats to Workplace Safety
- 1. Slip and fall
- 2. Struck by moving object
- 3. Struck against stationary objects
- 4. Overexertion
- 5. Repetitive motion injuries
- 6. Electrocution
- 7. Entanglement
- 8. Motor vehicle accidents
- 9. Falls from heights
- 10. Workplace violence
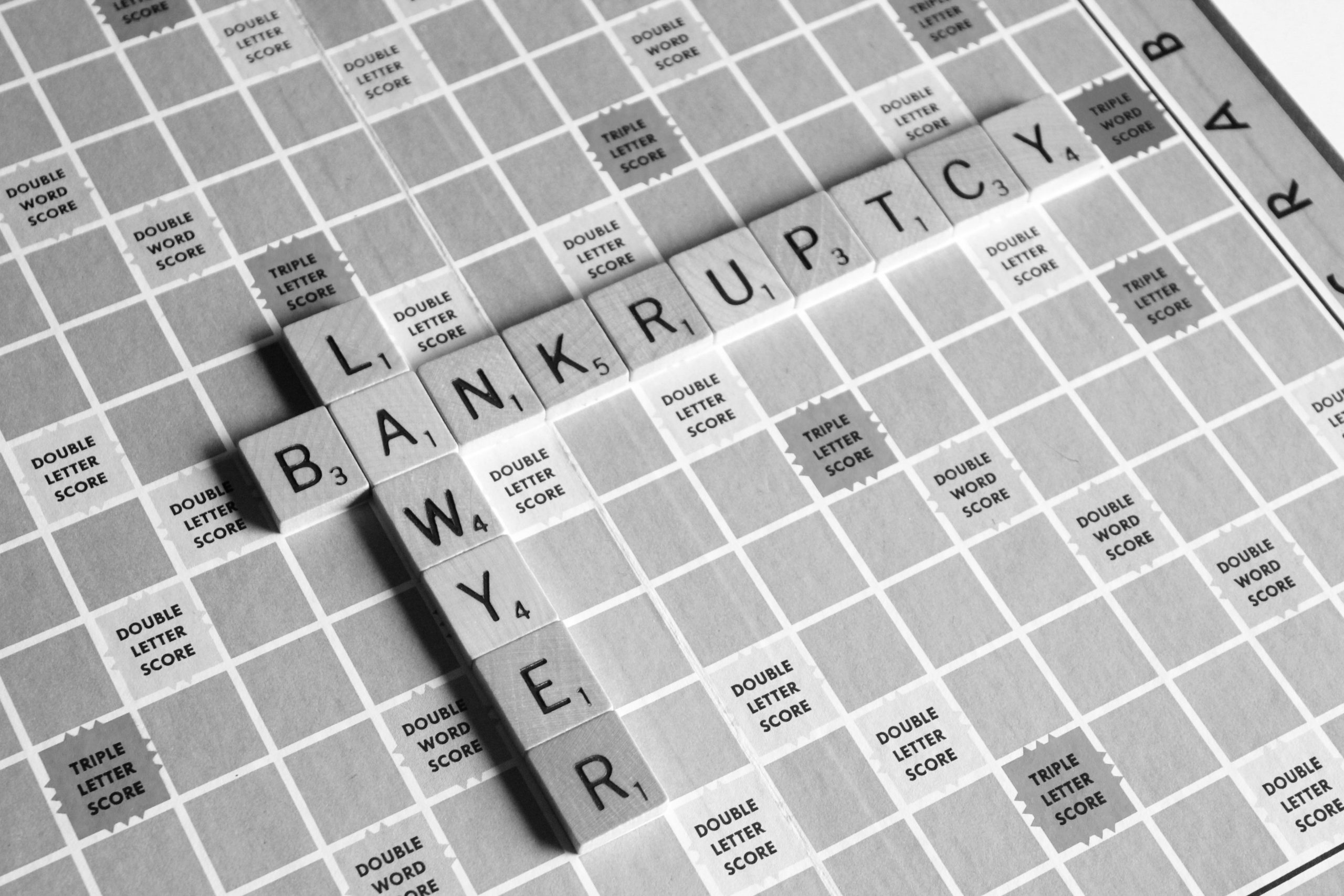
Not incorporated within these incidents is the workplace risks created by the COVID-19 pandemic. While the COVID-19 virus has not been classified as an OSHA-covered hazard, workplaces have to be diligent in their efforts to maintain safety with social distancing and Personal Protective Equipment (PPE).
Employees need easy-to-access resources to recognize and refresh risk management standards in their field. Create a centralized location with tangible OSHA guidelines and steps to prevention to ensure active learning and education are working towards a safer work environment for employees and customers alike.
Understand the Risks of Non-Compliance
- Financial burden: OSHA fines for non-compliance and workplace incidents can run anywhere from $13,000 to $130,000. Repeat and willful penalties are enough to put serious financial constraints on any business and doesn’t include the legal costs that often come with employee incidents. Workers’ compensation settlements average $21,800 and can cause insurance premiums to soar.
- Employee and customer safety: When OSHA standards are weakened or disregarded within workplaces, employees and customers can be exposed to serious hazards, injuries, and illnesses. Even among reasonable or unavoidable workplace accidents, the fallout can potentially thwart future employee and customer satisfaction.
- Damaged reputation: Litigation, press coverage, and whistleblowing can quickly make an OSHA violation into a public relations disaster. Lost revenue and diminished customer buy-in often outweigh the direct, financial responsibilities of OSHA violations.
Build A Culture of Reporting
Keep OSHA standards within easy access for employees supports active prevention for the issues relevant to your organization. This starts with an all-in-one resource and reporting tool, which enables staff to proactively identify areas of potential risk before accidents occur¾and easily report them and track all incident data to maintain compliance.
Relying on robust software for this crucial task, automated reporting frees up your team to focus on minimizing risk, rather than the labor-intensive process of documenting claims. According to one CIP Reporting customer from a large logistics provider, the need for a solution that would help employees shift focus to preventative measures directed at reducing claims, incidents, and losses was critical to save time and resources, and get employees back to high-value work.
Modern solutions enable companies to generate OSHA location-specific reports for any number of locations saving organizations tremendous time and overhead. Clients describe that the structural support created by CIP Reporting has fostered a culture of reporting that makes team members accountable and better equipped to execute risk management, prevention, and documentation with confidence.
“My team has gone from managing roughly 30 reports to more than 300 reports each month. With CIP Reporting, my team is not only able to manage this increase in volume, but we have great confidence that each issue is being handled appropriately, and any gaps are being closed.”– Melissa Miller, Quality Improvement Manager at Woodcreek Provider Services
CIP Reporting reduces the risk of human error by ensuring all communications and incident information is tracked and recorded, escalated to the appropriate parties, and compiled and submitted, and accessible for executives to identify trends, prevention methods, and other insights that improve risk management. For more information on how CIP Reporting can improve your workplace safety, click here.